Bette Barnett - Studio Migoto, USA
Bette Barnett is the owner of Studio Migoto, in La Mesa, California, where she is recognized for her expertise in steel with gold utilizing Keum Boo techniques. Bette holds a B.S. in education and journalism from North Texas University and spent a career working as a corporate communication consultant before transitioning to jewelry-making in 2010. She is an avid jewelry instructor at her private studio and in workshops around the United States, including Sawtooth School for Visual Arts, Metalwerx School for Jewelry, Mendocino Art Center and Creative Side Jewelry Academy. Bette has published articles on steel and gold in Lapidary Journal Jewelry Artist magazine. This is her first presentation at the Santa Fe Symposium®.
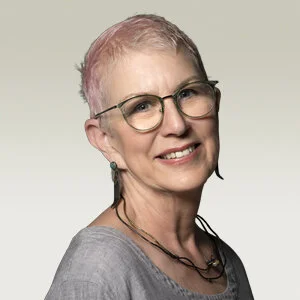
This paper expands the current body of knowledge about mild (low-carbon) steel and fused gold by exploring innovations such as fusing silver, copper, shakudo, shibuichi and various alloys to steel. It summarizes results of comparative experiments identifying best practices for working with steel including annealing, forming, soldering, patination and sealing the steel. In addition, it examines the feasibility of fusing a wide range of metals and alloys to steel and assesses their coverage, flow, finish and color. The paper goes on to explore methods to control and limit the flow of fused gold and other metals across the surface of steel. It discusses the efficacy and processes involved in diffusion and mechanically bonding metals to steel including keum-boo. Finally, various steel patination methods to determine intensity, color and durability will be compared and preferred methods for application will be shared.
Dr. Carlo Burkhardt - Pforzheim University, Germany
Dr. Carlo Burkhardt holds a Ph.D. in metallurgy and materials from the University of Birmingham, UK, and is the current scientific director at the STI–Institute of Jewelry Technology and professor of manufacturing technologies at Pforzheim University in Baden-Württemberg, Germany. He has coordinated several large European Union-funded research and development projects with budgets exceeding €20 million. Carlo is the recipient of the European Powder Metallurgy Association (EPMA) Powder Metallurgy Thesis Award in 1993, the German Raw Materials Efficiency Prize in 2017 and the Baden-Württemberg Environmental Technology Award (material efficiency category) in 2017. Carlo has authored three books, published more than 20 peer-reviewed papers and holds several patents. This is his first presentation at the Santa Fe Symposium®.

In order to overcome existing constraints in the in-service behavior of currently available additive manufacturing (AM) materials, an advanced production method for high-performance technology metals was developed based on a modified vat polymerization-based (VP) printing for metal powders. The new, innovative lithography-based metal manufacturing (LMM) process is able to photo-harden a photopolymeric binder that is highly filled with metal powder.
After debinding and sintering, the fully dense metal AM parts will provide various advantages such as superior properties with respect to cracks or internal stress when compared to laser-based powder bed fusion (L-PBF) AM parts. LMM is suitable to build very detailed, complex structures with a minimum of after treatments and without need for support structures. The LMM parts exhibit superior surface quality, are less demanding with respect to powder particle size/morphology and allow effective re-use of the feedstock materials.
The LMM process will be explained in detail. Its suitability for the production of jewelry and watch cases will be demonstrated for stainless steel-type materials and titanium alloys on various samples. Finally, an outlook for precious metal powders will be given.
Frank Cooper - Birmingham City University School of Jewellery, U.K.
Frank Cooper is a life-long jewelry industry professional and associate head of the Birmingham School of Jewellery, where he is a senior lecturer in jewelry manufacturing technologies and manager of the Centre for Digital Design and Manufacturing. He sits on the Goldsmiths’ Craft and Design Council and is the chair of a committee reporting back to the government via Innovate UK about industry needs for the up-skilling of technological skills, education and training in the additive manufacturing and 3D printing sphere. Frank is a globally recognized expert in the application of various additive manufacturing and prototyping/3D printing technologies used in the jewelry industry and has published and presented many technical papers and articles around the world. He is a recipient of the Santa Fe Symposium® Ambassador and Business Innovation Awards. This is his sixth presentation at the Symposium.
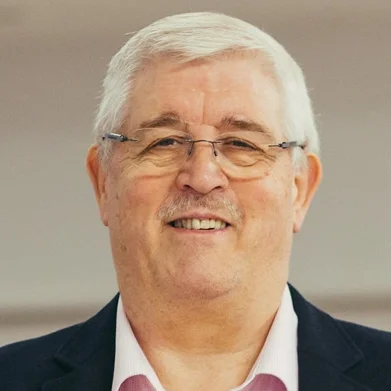
Following the seminal paper and presentation at the 2019 Santa Fe Symposium® by Nanz Aalund and Charles Lewton-Brain entitled “Jewelers: The Next Generation,” I came back to my own School of Jewellery in the UK, determined to reappraise and reassess with fresh eyes all those things I have taken for granted over the many years I have worked at the school.
This paper will consider the place of the Birmingham School of Jewellery within its historical context of 130 years of teaching jewelry and silversmithing in the heart of the Birmingham Jewellery Quarter (BJQ). It will examine the evolution of instruction over the years to where we now teach our students both traditional artisanal craft techniques alongside advanced twenty-first century digital technologies across a number of degree, and non-degree, courses to our nearly 400 students, a student body that continues to grow. We will consider, course by course, what we teach, how we teach and why we teach. We will consider both home and international students as well as our small part-time study group and give an overview of our burgeoning Ph.D. and post-doctoral programs.
Dr. Christopher W. Corti - COReGOLD Technology Consultancy, U.K.
Dr. Corti holds a Ph.D. in metallurgy from the University of Surrey (UK) and is the managing director of COReGOLD Technology Consultancy. He has more than 40 years of experience in the precious metals industry. He worked for the World Gold Council from 1994 to 2004 and served as a consultant there until 2009. Chris edited Gold Technology, Gold Bulletin and the series of World Gold Council handbooks/manuals. He is currently a consultant for the Worshipful Company of Goldsmiths in London and edits the Goldsmiths’ Company Technical Bulletin. A recipient of the Santa Fe Symposium® Research, Technology, Ambassador and Lifetime Achievement Awards, Dr. Corti has presented at the Symposium for 24 years.

In the previous three parts of this series, we examined the relationship between properties, microstructure and alloy composition and the defects that can arise during manufacture. In this fourth part, we will examine hot and cold working in a little more detail and relate them to control of microstructure and, hence, properties. We will also look at joining processes, particularly soldering and welding, used in jewelry manufacture and finish with some comments on corrosion and tarnishing and how we can influence these by alloying and microstructure control.
Ettore Maurizio Costabeber - DWS S.r.l, Italy
Ettore “Maurizio” Costabeber is a 20-year industry-leading expert and entrepreneur for 3D printing technology and design, and rapid prototyping. He pioneered and launched the first model of a 3D desktop printer in 1993, introduced the first 3D SLA desktop printer, E-DARTS, in 1998 and is the current chief technology officer at Digital Wax Systems (DWS) Srl in Thiene, Italy. Maurizio earned his M.B.A. at the CUOA Business School in Altavilla Vicentina, Italy and has authored more than 100 patents in the field of 3D printing. His DFAB 3D printer recently earned a Red Dot Award for Product Design (category Best of the Best) in 2018 and a Big See Product Design Award in Slovenia in 2019, while the XFAB 3D printer took home the Compasso d’Oro award (honorable mention) in 2018. This is his first presentation at the Santa Fe Symposium®.
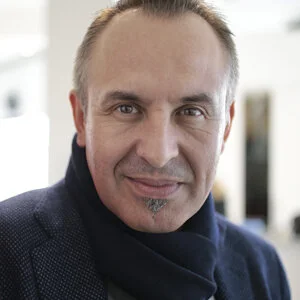
Conventional casting processes adopt a classic tree geometry layout, which was conceived for manual wax welding and assembly. Although this method is universally recognized as the main mass-production technology for jewelry manufacturing, it has many limitations in terms of efficiency and costs. A new casting tree concept may provide relevant savings in terms of precious metal use and refining. Additionally, the adoption of new software algorithms and advanced 3D printing technologies provides a fully digital process workflow, giving the manufacturer the advantage of producing any product mix and quantity with maximum freedom. Through this new concept, the manufacturer produces the right products at the right time, eliminates stock and reduces tied-up capital, thus building a direct link from customers’ needs to the factory.
Keith Donaldson - Engineered Materials, Inc., USA
Keith Donaldson is the president of Engineered Materials, Inc. in Buffalo Grove, Illinois. He holds a B.S. in chemistry and chemical engineering from Wayne State University and an M.S. in engineering management from Northwestern University. He holds five patents and has developed numerous products in several fields including electronics, medical, automotive, termite repellant and aerospace. Keith is a board member of Masters of Engineering Management at Northwestern University. This is his fifth presentation at the Symposium.
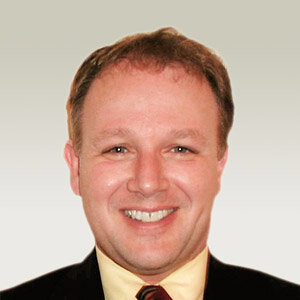
A study of corrosion on a series of silver rings will be presented, discussing causes of tarnish but also providing methodology for isolating individual parts of the packaging (dissecting the packaging and using each part in a corrosion study) and using them individually to determine their impact on tarnishing of the product. The methodology employed can be utilized by companies with limited equipment and generally found in production operations. A general review of materials commonly used in packaging will also be provided, highlighting techniques to use to determine their impact on increasing or causing tarnish. Active anti-tarnish packaging materials will also be reviewed in the context of how they work.
Dr. Joerg Fischer-Buehner - Legor Group S.p.A., Italy
Dr. Fischer-Buehner holds a diploma and a Ph.D. in physical metallurgy and materials technology from Technical University of Aachen, Germany. Since 2007 he has been active in research and development with Legor Group S.p.A., Italy, Indutherm GmbH, Germany, and BluePower Casting Systems GmbH, Germany. He was formerly head of the Physical Metallurgy and Precious Metals Research division of the Research Institute for Precious Metals & Metal Chemistry in Schwaebisch Gmuend, Germany. He is a recipient of the Santa Fe SymposiumÒ Research (two times), Ambassador, Outstanding Technical Presentation, Applied Engineering, and Collaborative Research (four times) Awards. This is his eleventh presentation at the Symposium.
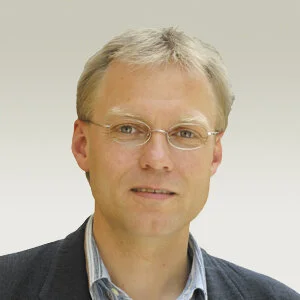
A new silver alloy has been developed with increased long-term tarnish resistance comparable to low-karat gold alloys and which requires no additional protective coatings. The paper reports on the alloy development, balancing hardness, manufacturing properties, tarnish resistance as well as metal costs (summarizing the results of an oral Santa Fe Symposium® presentation given in 2015). Results of accelerated lab tarnish tests are presented and compared with extensive real-life, long-term wear tests. Finally, examples of manufacturing trials from cooperating jewelry and watch manufacturers are presented, with a special focus on casting properties of the new silver alloy (silicon- and germanium-free) compared to regular sterling silver and fire scale-resistant alloys. The outcomes are discussed, keeping in mind consumer expectations and market approach.
Teresa Fryé – Techform, USA
Teresa Fryé is the founder and president of TechForm Advanced Casting Technology. In the early 1990s her firm introduced high-temperature casting methods from the aerospace industry to platinum manufacturing. A leading expert on shell casting methods and a prolific researcher, she has published technical papers and articles worldwide. Her publications have appeared in the Proceedings of the Santa Fe Symposium, the Johnson Matthey Technology Review, the Jewelry Technology Forum, the Jewellery Materials Congress, the MJSA Journal, and JCK Magazine, among others. She has also presented her research at numerous venues across the globe. Her company TechForm has been providing platinum castings to a broad customer base, including most of the top jewelry brands in the US for over 25 years. In addition to her manufacturing business, in 2008 Teresa founded the Portland Jewelry Symposium, an annual educational conference that serves the educational needs of manufacturing jewelry retailers and designers. She is a two-time recipient of the Santa Fe Symposium® Ambassador Award and a five-time recipient of the Collaborative Research Award. This is her sixth year presenting at the Symposium.
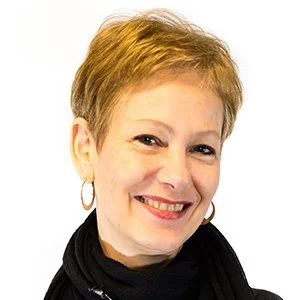
A series of iterative wear and corrosion tests were conducted on two 950 platinum alloys, two 585 white gold alloys and two 750 white gold alloys. Testing followed standardized industrial procedures in order to provide comparable and reproducible conditions. Wear testing comprised a sequence including abrasion testing, corrosion testing and polish testing. Mass loss was recorded after each test cycle. Five complete test cycles were followed by two long-term polish tests. The total testing time was ca. 250 h. A pronounced difference in the mass and volume loss between the platinum and the gold alloys was observed. The absolute volume loss per surface area of the platinum alloys was a factor of two to three times lower than that of the gold alloys. The highest volume loss was observed for 750AuPd, followed by 585AuPd, 585AuNi and 750AuNi, with the latter three showing similar wear behaviors. The mass loss increased linearly with testing time. No measurable mass loss was observed by corrosion testing in our limited duration test cycle and the only alloy exhibiting significant corrosion was 585AuNi. Hardness of the alloys was determined by Vickers microhardness testing at a 100 g load. Notably, higher hardness levels were not found to be an indicator for low mass or volume loss.
Franz Held - Research Institute for Precious Metals and Metals Chemistry (fem), Germany
Franz Held studied metallography at the Max-Planck Institute in Stuttgart, Germany. For the past 20 years, he has held a laboratory technician position involved in research projects at the Department of Physical Metallurgy at the Research Institute for Precious Metals & Metal Chemistry in Schwaebisch Gmuend, Germany. Franz is a metallographer, material tester, economist, and certified Quality Management Auditor. He has worked for different metal refiners and has vast experience in research and testing. This is his third presentation at the Symposium.

Additive manufacturing continues to gain increasing importance for the production of technical products. Powder-bed additive manufacturing that uses a laser heat source is most widely used and has been applied to gold and platinum alloys in the past. Material properties such as porosity and surface roughness play an important role in final part quality. This paper will describe the effect of different materials’ properties and process parameters on the results obtained with additive manufacturing. The different materials include steel, titanium, copper, gold and platinum alloys, which have a wide range of important properties such as reflectivity, surface tension of the liquid, and thermal conductivity. Tests were done using many process parameters employing machines that are currently used in the jewelry industry by different manufacturers. The paper will promote understanding of the correlation of machine type, process parameters and material properties in order to improve the final quality of additively manufactured parts.
Dr. David Huycke - PXL-MAD School of Arts, Hasselt University, Belgium
Dr. David Huycke is an internationally renowned Belgian silversmith, a professor at the PLX-MAD School of Arts, in Hasselt, Belgium and a professor at the Faculty of Architecture and Arts at Hasselt University. He holds an M.F.A. in jewellery design and silversmithing from Sint-Lucas University College in Antwerp, Belgium and a Ph.D. in arts from Hasselt University and Katholieke Universiteit Leuven. A two-category recipient of the first Henry Van De Velde Awards (young talent prize and prize of the public categories) by Flanders DC in Brussels in 1994, David has also been awarded the European Prize for Contemporary Art- and Design-led Crafts (younger than 35 years category), WCC-Europe, in Vienna in 1998 and the gold medal for the Bavarian State Prize (contemporary crafts category), International HandwerksMesse, in Munich in both 2007 and 2019. His work has been displayed in national and international galleries and museums, and he has permanent collections in the Design Museum Gent (Ghent, Belgium), the Victoria and Albert Museum (London), Deutsche Goldschmiedehaus Hanau (Hanau, Germany) and the Indianapolis Museum of Art. David is known for his modern artistic relevance on the ancient technique of granulation. This is his first presentation at the Santa Fe Symposium®.
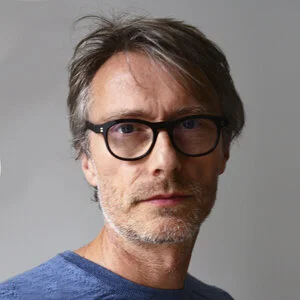
Granulation is an ancient technique in goldsmiths' art where little balls decorate surfaces with ornamental and figurative patterns. Because of its specific nature, granulation was, and still is, rarely used in a larger scale. This paper suggests two different applications of silver granulation in larger scale: first in the well-known method as a decorative technique and second as a constructive technique, where the little granules build the artefact and form structure and decoration at the same time. Both methods have specific problems which will be discussed and unraveled. The development of new tools and the entire working processes will be presented—the production of larger granules, the silver alloys used, the application of the copper (oxide), and the reaction-soldering of silver—in both decorative and constructive ways.
Owain Houghton - University of Cambridge, U.K.
Owain Houghton is a Goldsmith’s Ph.D. student researching bulk metallic glasses based on precious metals at the University of Cambridge, UK. He received a M.Sci. in materials science and a B.A. in natural sciences at the same university. During his schooling he has received two departmental undergraduate awards: Part 1A Rolls-Royce Materials Prize and Part II CEGB Prize. This is Owain’s first presentation at the Santa Fe Symposium®.
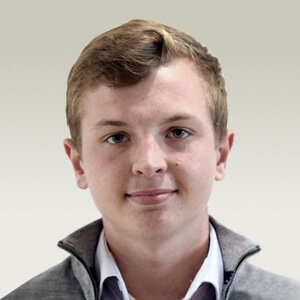
Bulk metallic glasses are a relatively novel class of materials which exhibit improved hardness over conventional crystalline alloys, high elasticity, lower casting temperatures, minimal shrinkage on casting, and thermoplastic formability. This translates into much-improved wear resistance without the need for extensive hot working, high definition near-net-shape casting, and processability via methods usually reserved for polymers and conventional oxide glasses. Consequently, bulk metallic glasses based on precious metals should be of significant interest for jewelry. However, issues regarding the abnormal tarnishing of 18K gold-based bulk metallic glasses remain. Hence, further research is still needed to preserve their desirable luster.
Bulk metallic glasses based on precious metals were discussed previously at the 2007 Santa Fe Symposium® by B. Lohwongwatana and at the 2013 Santa Fe Symposium by U. Klotz. Here, more recent developments are reported, alongside current research into tarnishing and further potential avenues of research.
Hugo Kohl - Hugo Kohl Fine Jewelry, USA
Hugo Kohl is president and curator of the Museum of American Jewelry Design & Manufacturing, owner of Hugo Kohl in Harrisonburg, VA and a highly skilled goldsmith specializing in contemporary designs from Industrial Age machines and traditional methods. Hugo earned his B.S. in finance and economics from James Madison University and formally apprenticed under a master goldsmith. He is a member of the board for The Providence Jewelry Museum and founder of HKmfg. This is his first presentation at the Santa Fe Symposium®.
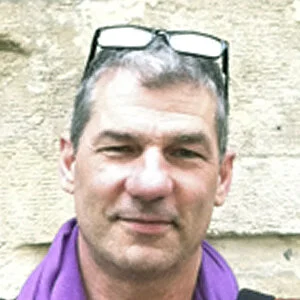
This paper will show how early Industrial Age jewelry design and manufacturing technology can be contemporized and put back into economic production by leveraging modern tools and materials. I will explain how I have collected and curated early American Industrial Age jewelry hubs, dies and rolls which are now used to make filigree rings that can compete in today’s marketplace. The significance of early 20th century Providence, Rhode Island, jewelry design and how principles guiding early tool makers can be combined with contemporary molding and casting technology to bring Providence-style filigree ring designs back to the marketplace will be discussed. The competitive challenges inherent in 1920s−1930s filigree ring making will also be explained.
Dr. Ulrich E. Klotz - Research Institute for Precious Metals & Metal Chemistry (fem), Germany
Dr. Ulrich Klotz is a diploma engineer in physical metallurgy (University of Stuttgart, Germany), holds a Ph.D. in materials science (ETH Zurich, Switzerland), and is currently head of the department of physical metallurgy at the Research Institute for Precious Metals & Metals Chemistry (fem), Schwaebisch Gmuend, Germany. His research work has included investment casting, casting simulation, phase diagram determination and modeling, micro/nanostructure investigations, alloy development, and brazing and soldering. Dr. Klotz is a two-time recipient of the Santa Fe Symposium® Research and Collaborative Research Awards. This is his tenth year presenting at the Symposium.
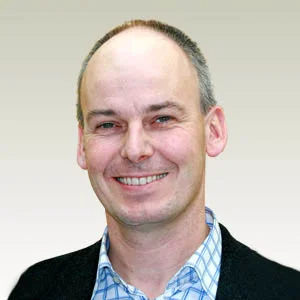
Titanium investment casting is extremely challenging due to the high reactivity of titanium melts. Current crucibles and investment materials are reduced by liquid titanium, resulting in a contamination of the melt and a deterioration of material properties. The paper describes the development of a new shell mold system and crucibles based on calcium zirconate ceramic. Tilt casting and centrifugal casting trials were run in different commercial casting machines on typical-sized jewelry trees. The results using the new ceramic material were compared to commercial shell molds and crucibles that work with a yttria front coat. The role of process parameters (casting conditions, flask temperature, etc.) was studied in detail for titanium grades 2 and 5 and other high-melting, highly reactive alloys. Investigation of the samples by metallography and SEM shows limited reaction with the ceramic and very limited surface hardening. Therefore, the new crucible/shell mold system appears promising for industrial application.
Charles Lewton-Brain - Retired, Alberta College of Art & Design, Canada
Charles Lewton-Brain, a master goldsmith, was educated in Germany, Canada and the United States. His writing on research into compositional systems in metal working and its results have been published internationally. He invented and disseminated foldforming, a system of working sheet metal that was new to the field. Charles has been recognized globally for his art work and received Canada’s highest honor for craft, The Saidye Bronfman Governor Generals Award. He was one of the founders of the Canadian Craft Federation, Canada’s national organization, and served as president for over two years. He co-founded the Ganoksin Project in 1996, now the world’s largest educational website for jewelers. Author of nine books and hundreds of articles, Charles has taught hundreds of workshops internationally. He is a recipient of the Santa Fe Symposium® Ambassador Award. This is his sixth presentation at this event.

This paper describes and names the types of chasing and repoussé tools used historically and across different cultures and times to create complex patterned and figurative surfaces on sheet and solid metal objects. This has not been done to this depth in other published work. It addresses tool purposes, procedural approaches and results. It reviews basic hardening and tempering for making a chasing tool. Historical sources are reviewed and addressed. The paper also addresses how to identify the shape of a tool from the mark on the chased metalwork, allowing the identification of tool forms and types from historical work. The case will be made that chased surfaces have a place in current production model-making as they provide detailed decorative and relief surfaces that have the “human” touch.
David Lindow - Lindow Machine Works, USA
David Lindow of Lake Ariel, Pennsylvania, is a clockmaker, owner of Lindow Machine Works, current vice president (and formerly president) of Ornamental Turners International, guest tutor at the Memoria Technica Workshop in Seattle and inventor of the MADE. lathe (a modern ornamental lathe). In 1990, David began a six-year apprenticeship with Gerhard Hartwigs, a master clockmaker. He took a brief break during this time and moved to Salt Lake City where he worked in a machine shop making and repairing parts for the salt and copper industries. David has built over 1,500 clock movements, 150 gear cutting machines, 115 rose engine lathes and has restored many period clocks. In 2000, David placed first (two-train clock movements category) at the National Association of Watch Collectors (NAWCC) Crafts Competition and in 2018 placed first (engraved metals category) and third (horological tools category) for the same competition. His work can be found in several institutions around the United States. This is his first presentation at the Santa Fe Symposium®.
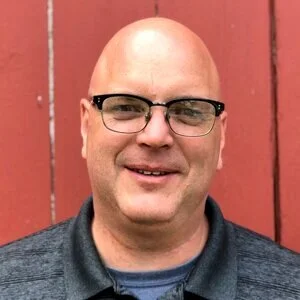
After a brief history of the lathe's development, the paper will explore various types of lathes used in jewelry manufacturing and various uses for those lathes that will not only improve on the possibilities in one's work but also show simple jigs and fixtures made on the lathe that can increase productivity. This paper will differentiate between types of lathes that are commonly available and will introduce the work best suited for each of them. Basic information on cutter geometry for both turning with the slide rest and hand turning will also be discussed.
Dr. Boonrat Lohwongwatana - Chulalongkorn University, Thailand
Dr. Boonrat Lohwongwatana holds a faculty position in the Metallurgical Engineering Department, Chulalongkorn University in Bangkok, Thailand. He earned a Ph.D. in materials science from the California Institute of Technology. He is the recipient of Thailand’s Young Technologist Award (2013) from HRH Princess Sirinthorn, and Thailand’s Young Metallurgist Award (2015). He received first place in the SCB Digital Venture Accelerator program in 2018. Boonrat collaborates with various jewelry companies in Thailand and internationally. He is the recipient of the Santa Fe Symposium Ambassador and Outstanding Technical Presentation Awards and is a two-time recipient of the Research Award. This is his eighth paper for the Symposium.
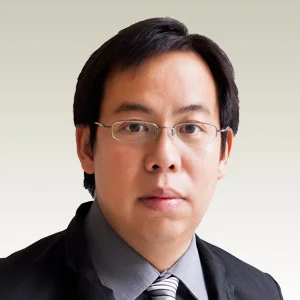
Throughout history, craftsmen and artisans have been striving for unique identities by introducing and perfecting techniques in jewelry manufacturing ranging from design, material selections, manufacturing methods, to finishing processes. Complexity of each jewelry item is a result of a combination of numerous artisan techniques such as casting, soldering, enameling, polishing, anodizing, cladding, laser welding, laser cutting, sintering, etc. The emergence of additive manufacturing (AM), also known as direct digital manufacturing (DDM), has already revolutionized various manufacturing sectors including medical, automotive, aerospace and jewelry. Known for its design flexibility and low cost for low-volume production, DDM is foreseen as an excellent prospect for new ideation in design and extreme complexity in design, as well as parts conglomeration. Other added benefits of DDM include ease of access to small and medium enterprises, micro-scale parts fabrication, automation in design, and streamlined and lean manufacturing. DDM of precious metal has become a key industrial and research focus in recent years. This paper presents overviews of digital manufacturing, highlighting current trends in DDM in various industries and how to apply them to the jewelry manufacturing line. New possibilities in design, modelling and fabrication of micro-scale jewelry architectures through conventional and DDM approaches are discussed. The extension of the paper explores the benefits and limitations of the DDM technologies, which might be further adapted in the jewelry industry for automation, lean manufacturing, and mass customization production.
Janjaap Luijt - Agandau Research, Netherlands
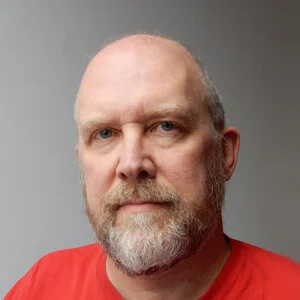
This paper discusses how new tools and techniques have influenced design and fashion. Examples will be shown from the Middle Ages up to the present day. You will learn about ancient gold and silversmith tools and techniques and understand why certain designs originated in their time and not earlier. You will also see how what we are using now results in the designs we make today.
Dippal Manchanda – Birmingham Assay Office and Anchorcert Group, U.K.
Dippal Manchanda, Technical Director and Chief Assayer of the Birmingham Assay Office and Anchorcert Group, is personally active in many metal allergy and metal testing research areas. He is a member and UK representative of CEN/TC 347/Task Group1 responsible for revising EN1811- Nickel release test standard and a member of the BSI STI/053, ISO/TC 174/WG 1 committee on jewellery. Dippal holds a master’s degree (MSc) in inorganic chemistry. He has over 35 years of experience in assaying and examining precious/non-precious metals, alloys, hazardous substances in jewellery, consumer goods and accessories. He is a Fellow of the Royal Society of Chemistry (FRSC), a Chartered Chemist (CChem) and a Chartered Scientist (CSci). He has been involved in several prestigious projects related to metal testing, metal allergy, manufacturing and precious metal refining. One of his recent projects was to develop an Anchorcert Pro (AP) test methodology to ascertain if the alloy material is safe for individuals with skin allergies.
In his role as Chief Assayer and Technical Director, Dippal is responsible for setting, managing and maintaining high analytical standards throughout the Assay Office and providing scientific and technical support on a day-to-day basis to both the statutory and non-statutory parts of the business. He has written, contributed to, and published a range of peer-reviewed scientific papers and presented at numerous international conferences during his career. This is Dippal’s second presentation at the Santa Fe Symposium®.
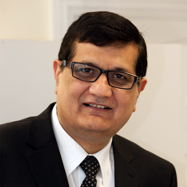
The ionization of elemental gold is essential to induce contact allergy and to elicit allergic contact dermatitis (ACD). It is understandable that gold, when present in a solution as a soluble or complex ion, may cause contact dermatitis. However, keeping the electrochemical nobility of gold in mind, it is not clear how metallic gold or gold alloys present in jewelry and similar products would react with body sweat at a rate sufficient to elicit an allergic reaction in gold-sensitized people. Notably, experiments in vitro with simulated sweat solutions have concluded little to no gold ion formation. Defining the role of gold in contact allergy has undoubtedly become a major challenge for dermatologists, as the evaluation of data presented in the literature regarding the release of gold in sweat is not conclusive.Less than two decades after gold was named “Contact Allergen of the Year” by the American Contact Dermatitis Society, research carried out at the Birmingham Assay Office AnchorCert Analytical Laboratory has now conclusively proven that, provided conditions are favorable, gold articles, both in plated and un-plated category, can react with bodily fluids such as sweat and release soluble gold ions which can potentially induce allergic contact dermatitis in gold-sensitized individuals. This paper provides an overview of the literature concerning gold allergy and gold-release data from various gold alloys and gold-plated materials, including those where gold release in sweat was conclusively detected and measured by the ICP-OES technique.We are continuing broader studies, conducted more rigorously, which are needed to firmly answer the questions raised in this paper regarding the condition and mechanism of gold dissolution in bodily fluids.
Anne B. Miller - Retired, IBM, USA
Anne Miller is a business transformation consultant and a Lean Six Sigma Black Belt. She is a recognized thought leader in business transformations that include strategy; methods and techniques; the application of technology to radically change processes, operations and organizational culture; and change management and adoption. Anne has delivered successful transformation projects with clients and within IBM for over three decades. Her awards include IBM Innovation and Excellence Award, IBM Eminence and Excellence Award (received twice), and the Santa Fe Symposium® Business Innovation and Ambassador Awards. Anne recently received recognition from Tiffany Manufacturing at their Technical Innovation Day. This is her ninth presentation at the Santa Fe Symposium.
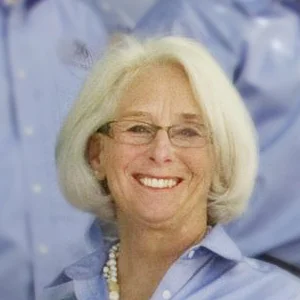
Responsible sourcing, proof of provenance and verifiable trust are becoming increasingly important to the jewelry industry. Today's consumers are more informed than ever before and expect transparency on the value and background of their purchase, with a willingness to pay more for sustainable goods. The ability to share the story of a piece of jewelry from mine to retailer is a competitive differentiator and resonates with customers. In addition, governments are targeting the jewelry industry to know and document the origins of all materials or be subject to additional regulations.
Blockchain is becoming an important solution to address the challenges of trust. This paper explores the realities of blockchain implementations to help the industry more fully understand how this technology addresses critical issues and what to expect from production applications. First-hand stories from the field will add context and dimension to deepen an appreciation for blockchain applications for jewelry manufacturing.
G. Phil Poirier - Bonny Doon Engineering, USA
G. Phil Poirier is the CEO of Bonny Doon Engineering in Taos, New Mexico, a company that develops and manufactures hydraulic presses and tooling systems for the jewelry industry. A true "smith" at heart (since his first silversmithing class in high school), Phil is a recognized designer, craftsman and engineer who has been maneuvering and manipulating metal into unimaginable forms for 47 years. He is a generous teacher who is the product of self-teaching and numerous apprenticeships and knows the value of hands-on learning. He is the recipient of the Reyna Award for Jewelry Excellence in 2012 and the Santa Fe Symposium® Ambassador, Jewelry Technology Leader, Outstanding Technical Presentation and Technical Innovation Awards. Phil is presenting for the eighth time at the Symposium.
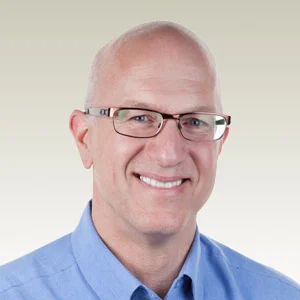
Many new ideas and techniques have been developed since the 2003 Santa Fe Symposium® paper, “Innovative Uses of the Hydraulic Press for Jewelry Manufacturing.” This paper will continue from that point with all the newest advances in hydraulic forming and will include tricks and techniques to more efficiently form jewelry metals. It will help you understand how to apply these ideas and processes to your own jewelry manufacturing line.
Dr. James Shigley - Gemological Institute of America, USA
Dr. James “Jim” Shigley is the distinguished research fellow at the Gemological Institute of America (GIA) where he has been employed for over 30 years. He earned his B.A. in geology from the University of California, Berkley and his Ph.D. in geology from Stanford University. An expert in gemological research, Jim has authored or co-authored 195 scientific articles and has received Gems & Gemology journal MVP award for more than 25 articles. He founded the GIA Gem Project and has scientifically developed methods of separating natural diamonds from laboratory-grown diamonds. Jim has been awarded the Edward J. Gübelin Most Valuable Article Award in 1998, the Accredited Gemologists Association Antonio Bonanno Award for Excellence in Gemology in 2007 and the American Gem Society’s Lifetime Achievement Award in 2017. Often recognized as the voice and face for GIA, Jim was presented GIA’s Richard T. Liddicoat Award for Distinguished Achievement—the thirteenth person ever to be honored with this award. This is his first presentation at the Santa Fe Symposium®.

Gem-quality synthetic diamonds are becoming increasingly available in the jewelry marketplace, and they have a place in the jewelry market as long as they are correctly identified and appropriately priced. Studies published over the past 30 years have resulted in an understanding of their production methods and means of identification. They can sometimes be recognized by a trained gemologist, but in the absence of distinctive visual features, positive identification requires examination by an experienced gem-testing laboratory. The traditional method of creating diamonds involves high pressure and temperature (HPHT) flux growth from a molten metal alloy to produce cuboctahedral-shaped crystals that have a flat base. The other method, called chemical vapor deposition (CVD), involves growth at high temperatures and very low pressures in a vacuum chamber to produce tabular crystals. Both methods can be used to produce colorless and colored synthetic diamond crystals. Differentiation of natural from synthetic diamonds is based upon recognizing the evidences of ancient growth and prolonged residence at high temperatures and pressures deep in the earth versus very recent and rapid growth of diamond in the laboratory or factory. Some of the instruments being developed for use by a jeweler to check for synthetic diamonds will be discussed.
Dr. Joseph Tunick Strauss - HJE Company, Inc., USA
Dr. Strauss is president and engineer of HJE Company, Inc. He holds a Ph.D. in materials engineering from Rensselaer Polytechnic Institute. He has authored more than 50 published works. He organized and co-chaired the Additive Manufacturing Powder Metallurgy Conference (AMPM) in 2014/2015 and again in 2020. He is a member of the Technical Committee of the Metal Powders Industries Federation (MPIF); the Minerals, Metals & Materials Society (TMS) Committee on Powder Materials; the ASTM Committee B09 on Metal Powders and Metal Powder Products and the ASTM Committee F42 on Additive Manufacturing Technologies. Joe teaches additive manufacturing in the annual MPIF PM Short Course and co-presents a tutorial on additive manufacturing at the annual MPIF PowderMet Conference. He
was chosen to write the chapter on MIM of Precious Metals for the Handbook of Metal Injection Molding and the chapter on Additive Manufacturing of Precious Metals for the ASM Handbook on Additive Manufacturing. He received the Distinguished Service Award by the Metal Powder Industries Federation and was awarded a Fellow of the American Powder Metallurgy Institute. Joe has also received the Santa Fe Symposium® Ambassador Award and is a two-time recipient of the Collaborative Research and Applied Engineering Awards. This is his twelfth year presenting at the Symposium.

There are several powder metallurgy-based manufacturing technologies that are in development or being practiced that have potential to significantly contribute to jewelry manufacturing. These include the traditional powder metallurgy technologies of press and sinter, metal injection molding (MIM), and hot pressing. The new non-fusion-based additive manufacturing technologies such as inkjet binding, inkjet printing, stereolithography, and extrusion methods will be discussed with their relevance to jewelry manufacturing. This paper will provide a review of powder metallurgy technologies and detail the current methods and applications of these technologies.
Dr. Alex Verdooren - Rio Grande, Inc., USA
Dr. Verdooren is currently a manufacturing engineer at Rio Grande and holds an M.Sc. and Ph.D. in chemical engineering from Lehigh University. He is a certified Six Sigma Green Belt from the American Society for Quality. This is his second presentation at the Symposium.
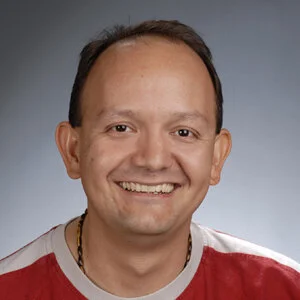
Mass finishing of discs and stampings can be very challenging. They are made out of precious materials that possess high specific gravity (8.9−16) and relatively low Vickers hardness (50−65 HV). These intrinsic properties can pose difficulties in the finishing operation due to the high risk of impingement.
This paper focuses on a particular case study on mass finishing. The aim is guiding the reader in how to use the Design of Experiments (DOE) tool. DOE is used to develop experiments that can collect sound statistical data. At the end of the day, the user can have a better understanding of the mass finishing process, because the main factors that affect good finishing are determined via DOE.
Damiano Zito – Progol3d S.p.A., Italy
Damiano Zito is the CEO of Progold S.p.A. in Trissino, Italy. He holds an M.B.A. from Fondazione Cuoa Business School, Vicenza, Italy. He has over 30 years of experience in the jewelry field. He is the chairman of the jewelry group at the Italian Standard Body UNI and is the head of the delegation of Italian experts participating in the working groups of the ISO 174 technical committee, “Jewellery and Precious Metals.” He is also an expert on CEN/TC347, “Method for Analysis of Allergens,” which is the technical committee for the nickel standard EN1811 and EN12472. Damiano is on the board of the Italian Jewellery Federation “Federorafi” with the rights for standardization and innovation. He is the recipient of the following Santa Fe Symposium® awards: Ambassador Award, Research Award, Business Innovation Award, a two-time recipient of the Applied Engineering Award, and his company’s R&D department is a four-time recipient of the Research Award. This is Damiano’s ninth year presenting at the Symposium.

In the past years, selective laser melting (SLMTM) disclosed new opportunities and possibilities for metal manufacturing, especially for those metals such as titanium and platinum alloys which are notoriously difficult to process through traditional production techniques. By using this innovative technology, jewelry manufacturing has been revolutionized, allowing the production of complex pieces with completely new designs and shapes as well as inspiring designer creativity. However, as a pencil has its own resolution limits in handwriting, the SLM technique has its own standard resolution limits as well.
This study aims to demonstrate how it has been possible to increase standard selective laser melting resolution in jewelry manufacturing, enabling sub-millimetric details on near-net-shape pieces. SLM resolution optimization was carried out by investigating and applying new printing strategies using commercial machines to produce jewelry parts. The representative parts were analyzed using optical and electron microscopy. The characterization scientifically demonstrates the great innovations and potential that can be achieved by improving the technique of selective laser melting for the jewelry manufacturing market.
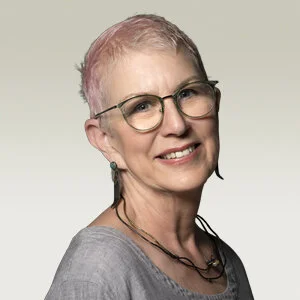

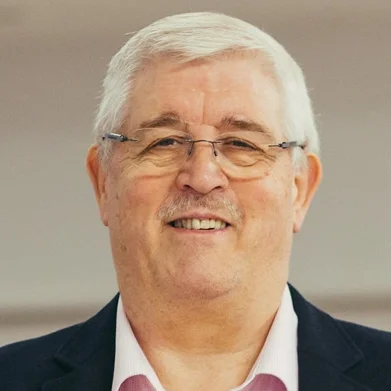

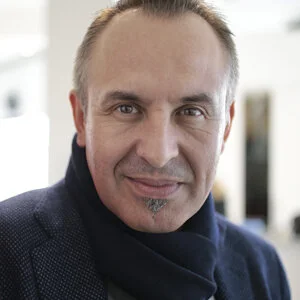
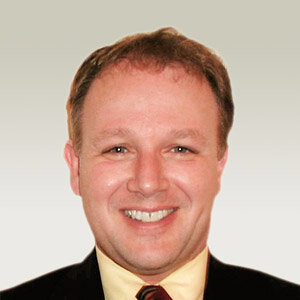
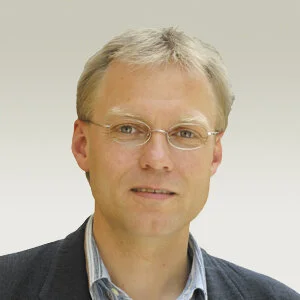
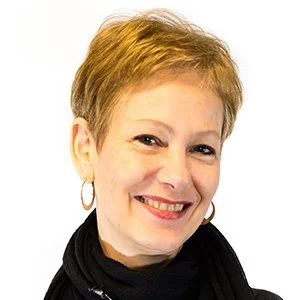

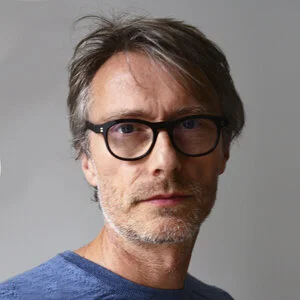
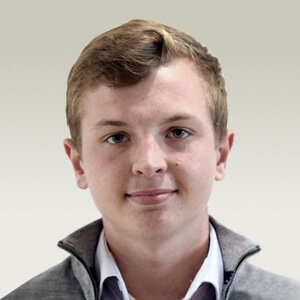
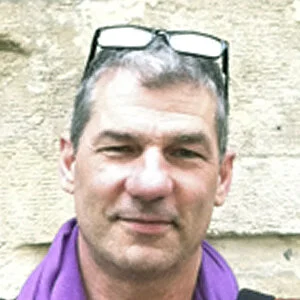


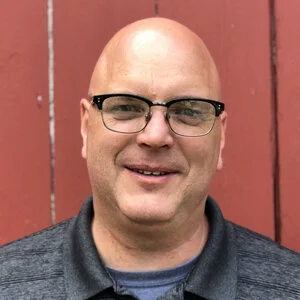

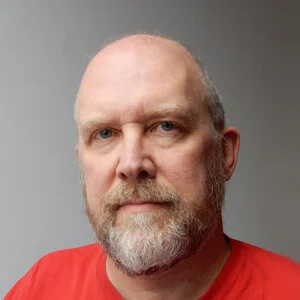
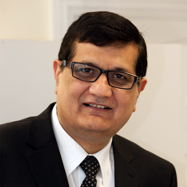
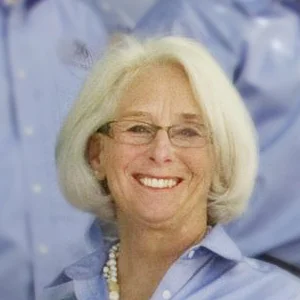
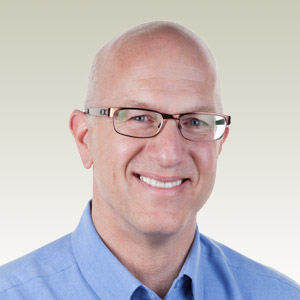

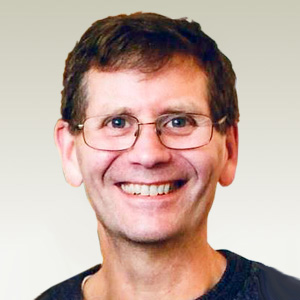
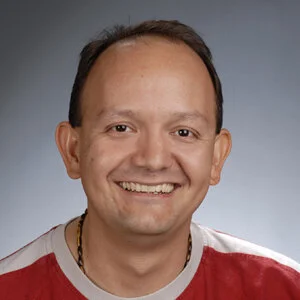
